el control de estabilidad (ESC)
El control de estabilidad es un elemento de seguridad activa del automóvil que actúa frenando individualmente las ruedas en situaciones de riesgo para evitar derrapes, tanto sobrevirajes, como subvirajes. El control de estabilidad centraliza las funciones de los sistemas ABS, EBD y de control de tracción.
El control de estabilidad fue desarrollado por Bosch en 1995, en cooperación con Mercedes-Benz y fue introducido al mercado en el Mercedes-Benz Clase S bajo la denominación comercial Elektronisches Stabilitätsprogramm.El ESP recibe otros nombres, según los fabricantes de vehículos en los que se monte, tales como Vehicle Dynamic Control ("control dinámico del vehículo", VDC), Dynamic Stability Control ("control dinámico de establidad", DSC), Electronic Stability Control ("control electrónico de establidad", ESC) y Vehicle Stability Control ("control de establidad del vehículo", VSC), si bien su funcionamiento es el mismo.
El sistema consta de una unidad de control electrónico, un grupo hidráulico y un conjunto de sensores:
sensor de ángulo de dirección: está ubicado en la dirección y proporciona información constante sobre el movimiento del volante, es decir, la dirección deseada por el conductor.
sensor de velocidad de giro de rueda: son los mismos del ABS e informan sobre el comportamiento de las mismas
sensor de ángulo de giro y aceleración transversal: proporciona información sobre desplazamientos del vehículo alrededor de su eje vertical y desplazamientos y fuerzas laterales, es decir, cual es el comportamiento real del vehículo y si está comenzando a derrapar y desviándose de la trayectoria deseada por el conductor.
El ESP® está siempre activo. Un microordenador controla las señales provenientes de los sensores del ESP® y las chequea 25 veces por segundo para comprobar que la dirección que desea el conductor a través del volante se corresponde con la dirección real en la que se está moviendo el vehículo. Si el vehículo se mueve en una dirección diferente, el ESP® detecta la situación crítica y reacciona inmediatamente, independientemente del conductor. Utiliza el sistema de frenos del vehículo para estabilizarlo. Con estas intervenciones selectivas de los frenos, el ESP® genera la fuerza contraria deseada para que el vehículo pueda reaccionar según las maniobras del conductor. El ESP® no sólo inicia la intervención de los frenos, también puede reducir el par del motor para reducir la velocidad del vehículo. De esta manera el coche se mantiene seguro y estable, dentro siempre de los límites de la física.
jueves, 30 de mayo de 2013
sábado, 25 de mayo de 2013
el sensor ckp y cmp
ckp
Para hablar del sensor CKP es necesario primero familiarizarse con el termino sensor de efecto Hall (denominado según Edwin Herbert Hall) se sirve del efecto Hall para la medición de campos magnéticos o corrientes o para la determinación de la posición.
El sensor CKP consiste en un cuerpo cilíndrico que en su
interior contiene un imán permanente, un centro metálico y una bobina
minúscula. Este sensor va montado cerca de un engrane dentado. A medida
que cada diente se mueve cerca del sensor, un pulso de
Corriente Alterna se induce en la bobina. Cada diente del engrane produce un pulso
eléctrico de Corriente Alterna, que es una señal análoga. A medida
que el engrane gira a mayor velocidad rotativa, se producen más pulsos, la ECU determina la velocidad giratoria del componente con base
en el número de pulsos. El número de pulsos que ocurren en un segundo
se conoce como la "frecuencia de la señal". De esta manera la ECU puede determinar información sobre la posición del cigüeñal y las RPM del motor.
Es muy importante la posición donde se ubique este sensor ya que cuando el sensor CKP se ubica muy alejado de los dientes del engrane, la lectura de pulsos será débil por lo tanto es muy probable que la lectura sea errónea y de lo contrario si el sensor CKP se ubica muy cerca de los dientes del engrane puede resultar dañado.
Este sensor se encuentra ubicado a un costado de la polea del cigüeñal.
Síntomas de falla
- El motor no arranca.
- No hay pulsos de inyección.
- Se enciende la luz check engine.
Cuando esto suceda se recomienda: Revisar los códigos de falla con la ayuda de un escáner, verificar si la punta del sensor está sucia de aceite o grasa y límpiarlo si es necesario, comprobar que las conexiones eléctricas de las líneas del sensor y del conector estén bien conectadas y que no presenten roturas o corrosión
cmp
El sensor de árbol de levas inductivo provee al PCM la información que le permite
identificar el cilindro numero 1. Es utilizado en los sistemas de inyección secuencial.
Es llamado también sensor de fase. Consta de una bobina arrollada sobre un núcleo
de imán. Este sensor esta enfrentado a un camón del árbol de levas y produce una
señal cada dos vueltas de cigüeñal. En algunos vehículos esta colocado dentro de el
distribuidor (Toyota).
El voltaje producido por el sensor del árbol de levas será determinado por varios
factores: la velocidad del motor, la proximidad del rotor de metal al sensor y la
fuerza del campo magnético ofrecida por el sensor. El ECM necesita ver la señal
cuando el motor se enciende para su referencia.
Las características de una buena forma de onda inductiva del sensor del árbol de
levas son: una onda alterna que aumenta de magnitud como se aumenta la
velocidad del motor y proporciona generalmente una señal por 720° de la rotación
del cigüeñal (360° de la rotación del árbol de levas). El voltaje será
aproximadamente 0.5 voltio al pico mientras que el motor está encendiéndose,
levantándose a alrededor 2.5 voltios de pico al pico en la marcha lenta según lo
considerado en la demostración del ejemplo.
ckp
Para hablar del sensor CKP es necesario primero familiarizarse con el termino sensor de efecto Hall (denominado según Edwin Herbert Hall) se sirve del efecto Hall para la medición de campos magnéticos o corrientes o para la determinación de la posición.
El sensor CKP consiste en un cuerpo cilíndrico que en su
interior contiene un imán permanente, un centro metálico y una bobina
minúscula. Este sensor va montado cerca de un engrane dentado. A medida
que cada diente se mueve cerca del sensor, un pulso de
Corriente Alterna se induce en la bobina. Cada diente del engrane produce un pulso
eléctrico de Corriente Alterna, que es una señal análoga. A medida
que el engrane gira a mayor velocidad rotativa, se producen más pulsos, la ECU determina la velocidad giratoria del componente con base
en el número de pulsos. El número de pulsos que ocurren en un segundo
se conoce como la "frecuencia de la señal". De esta manera la ECU puede determinar información sobre la posición del cigüeñal y las RPM del motor.
Es muy importante la posición donde se ubique este sensor ya que cuando el sensor CKP se ubica muy alejado de los dientes del engrane, la lectura de pulsos será débil por lo tanto es muy probable que la lectura sea errónea y de lo contrario si el sensor CKP se ubica muy cerca de los dientes del engrane puede resultar dañado.
Este sensor se encuentra ubicado a un costado de la polea del cigüeñal.
Síntomas de falla
- El motor no arranca.
- No hay pulsos de inyección.
- Se enciende la luz check engine.
Cuando esto suceda se recomienda: Revisar los códigos de falla con la ayuda de un escáner, verificar si la punta del sensor está sucia de aceite o grasa y límpiarlo si es necesario, comprobar que las conexiones eléctricas de las líneas del sensor y del conector estén bien conectadas y que no presenten roturas o corrosión
cmp
El sensor de árbol de levas inductivo provee al PCM la información que le permite
identificar el cilindro numero 1. Es utilizado en los sistemas de inyección secuencial.
Es llamado también sensor de fase. Consta de una bobina arrollada sobre un núcleo
de imán. Este sensor esta enfrentado a un camón del árbol de levas y produce una
señal cada dos vueltas de cigüeñal. En algunos vehículos esta colocado dentro de el
distribuidor (Toyota).
El voltaje producido por el sensor del árbol de levas será determinado por varios
factores: la velocidad del motor, la proximidad del rotor de metal al sensor y la
fuerza del campo magnético ofrecida por el sensor. El ECM necesita ver la señal
cuando el motor se enciende para su referencia.
Las características de una buena forma de onda inductiva del sensor del árbol de
levas son: una onda alterna que aumenta de magnitud como se aumenta la
velocidad del motor y proporciona generalmente una señal por 720° de la rotación
del cigüeñal (360° de la rotación del árbol de levas). El voltaje será
aproximadamente 0.5 voltio al pico mientras que el motor está encendiéndose,
levantándose a alrededor 2.5 voltios de pico al pico en la marcha lenta según lo
considerado en la demostración del ejemplo.
el ks
Este sensor usa un disco muy delgado de cerámica piezo-eléctrica, el cual esta unido a un diafragma metálico.
Este dispositivo algunas veces se llama resonador, cuando el golpeteo del motor es detectado por el diafragma metálico este aplica y libera presión del disco piezo-eléctrico, a la frecuencia del golpeteo del motor.
Un golpeteo mas fuerte provoca que el diafragma aplique una mayor presión al disco piezo-eléctrico. El disco responde con una mayor salida de voltaje.
Un sensor de pistoneo o detonación es un dispositivo piezo-eléctrico pequeño, que junto con el PCM, identifica estas detonaciones. El PCM ante esta circunstancia retrasara el encendido para evitar daños al motor.
La frecuencia de detonación (pistoneo) es aproximadamente 15 KHZ.
El punto óptimo en la cual la alta tensión (AT) enciende la mezcla aire/combustible será momentos antes del PMS, pero a veces será inevitable que bajo ciertas condiciones ocurra una detonación imprevista. Para medir esta señal se utilizara el osciloscopio con un barrido horizontal de 50 ms por división y una amplitud de tensión alterna pico a pico de 2V por división.
La mejor manera de probar un sensor de detonación, es quitar el sensor del motor y golpearlo ligeramente con una llave de tuercas pequeña, la forma de onda resultante debe ser similar al ejemplo demostrado.
Al reinstalar el sensor se debe apretar con el torque correcto indicado por el manual.
La comprobación de este sensor es solamente con osciloscopio dado que esta construido por un cristal piezo-eléctrico y no se puede medir su resistencia.
La comprobación de este sensor es solamente con osciloscopio dado que esta construido por un cristal piezo-eléctrico y no se puede medir su resistencia.
Este sensor es capaz de producir una señal debida a una vibración diferente a la normal provocada por un proceso de combustión detonante, con el objetivo de obtener la mayor potencia posible del motor con el menor consumo de combustible, se trata de obtener máximas presiones de trabajo en la cámara de combustión.
Este objetivo sin embargo se ve disminuido debido a las condiciones altamente variables bajo las cuales debe funcionar un motor, hace casi imposible el máximo aprovechamiento si no se utiliza un sensor de detonación, a través del cual la unidad de control puede variar el avance del encendido.
Este sensor consta de una cabeza metálica dentro de la cual se encuentra montada una pieza de cristal piezo-eléctrica que tiene la particularidad de generar una corriente eléctrica cuando es sometida a esfuerzos mecánicos.
Este objetivo sin embargo se ve disminuido debido a las condiciones altamente variables bajo las cuales debe funcionar un motor, hace casi imposible el máximo aprovechamiento si no se utiliza un sensor de detonación, a través del cual la unidad de control puede variar el avance del encendido.
El sensor de detonación es un dispositivo electronico capaz de medir la vibración y convertir esta señal en una salida eléctrica que mide el golpeteo del motor.
El sensor esta diseñado para vibrar aproximadamente a la misma frecuencia que el golpeteo del motor. El acelerador convierte la señal de vibracion en una salida eléctrica.
Este dispositivo algunas veces se llama resonador, cuando el golpeteo del motor es detectado por el diafragma metálico este aplica y libera presión del disco piezo-eléctrico, a la frecuencia del golpeteo del motor.
Un golpeteo mas fuerte provoca que el diafragma aplique una mayor presión al disco piezo-eléctrico. El disco responde con una mayor salida de voltaje.
frenos abs
El sistema antibloqueo de ruedas o frenos antibloqueo, del alemán Antiblockiersystem (ABS), es un dispositivo utilizado en aviones y en automóviles, que hace variar la fuerza de frenado para evitar que los neumáticos pierdan la adherencia con el suelo.
El sistema fue desarrollado inicialmente para los aviones, los cuales acostumbran a tener que frenar fuertemente una vez han tomado tierra. En 1978 Bosch hizo historia cuando introdujo el primer sistema electrónico de frenos antibloqueo. Esta tecnología se ha convertido en la base para todos los sistemas electrónicos que utilizan de alguna forma el ABS, como por ejemplo los controles de tracción y de estabilidad.
A día de hoy alrededor del 75% de todos los vehículos que se fabrican en el mundo, cuentan con el ABS. Con el tiempo el ABS se ha ido generalizando, de forma que en la actualidad la gran mayoría de los automóviles y camiones de fabricación reciente disponen de él. Algunas motos de alta cilindrada también llevan este sistema de frenado. El ABS se convirtió en un equipo de serie obligatorio en todos los turismos fabricados en la Unión Europea a partir del 1 de julio de 2004, gracias a un acuerdo voluntario de los fabricantes de automóviles. Hoy día se desarrollan sistemas de freno eléctrico que simplifican el número de componentes, y aumentan su eficacia.
En el año 1936 se patentó la idea por parte de la compañía alemana Bosch. Se trataba de hacer (no sólo para coches, sino también para camiones, trenes y aviones) que fuera más difícil bloquear una rueda en una frenada brusca, con lo que se podía conseguir una mayor seguridad. Se hicieron pruebas, pero no se llegó a nada serio hasta que se desarrolló la electrónica digital a comienzos de los años '70. Hasta entonces, era materialmente imposible realizar tantos cálculos como necesitaba el sistema y de forma rápida.
Bosch inició el trabajo en serio para el desarrollo del ABS en el año 1964 de la mano de una subsidiaria, Teldix.Pero es en 1970 cuando la firma desarrolla un dispositivo eficaz y con la posibilidad de comercializacion a gran escala. La primera generación del ABS tuvo 1.000 componentes, cifra que se redujo hasta 140 en la segunda generación. Después de 14 largos años de desarrollo, finalmente estuvo preparado el ABS de segunda generación, que se ofreció como una exuberante y revolucionaria opción en el Mercedes-Benz Clase S de la época junto con la Mercedes-Benz Clase E y en seguidas por el BMW Serie 7.
el vss
El sensor de velocidad del vehículo VSS (Vehicle Speed Sensor) es un captador magnético, se encuentra montado en el transeje donde iba el cable del velocímetro.
El VSS proporciona una señal de corriente alterna al ECM la cuál es interpretada como velocidad del vehículo.
Este sensor es un generador de imán permanente montado en el transeje.
Al aumentar la velocidad del vehículo la frecuencia y el voltaje aumentan, entonces el ECM convierte ese voltaje en Km/hr, el cual usa para sus cálculos. Los Km/hr pueden leerse con el monitor OTC.
El VSS se encarga de informarle al ECM de la velocidad del vehículo para controlar el velocímetro y el odómetro, el acople del embrague convertidor de torsión (TCC) transmisiones automáticas,
en algunos se utiliza como señal de referencia de velocidad para el control de crucero y controlar el motoventilador de dos velocidades del radiador.
Tiene en su interior un imán giratorio que genera una onda senoidal de corriente alterna directamente proporcional a la velocidad del vehículo.
Por cada vuelta del eje genera 8 ciclos, su resistencia debe ser de 190 a 240 Ohmios.
Con un voltímetro de corriente alterna se checa el voltaje de salida estando desconectado y poniendo a girar una de las ruedas motrices a unas 40 millas por hora. El voltaje deberá ser 3.2 voltios.
El sensor de velocidad del vehículo VSS (Vehicle Speed Sensor) es un captador magnético, se encuentra montado en el transeje donde iba el cable del velocímetro.
El VSS proporciona una señal de corriente alterna al ECM la cuál es interpretada como velocidad del vehículo.
Este sensor es un generador de imán permanente montado en el transeje.
Al aumentar la velocidad del vehículo la frecuencia y el voltaje aumentan, entonces el ECM convierte ese voltaje en Km/hr, el cual usa para sus cálculos. Los Km/hr pueden leerse con el monitor OTC.
El VSS se encarga de informarle al ECM de la velocidad del vehículo para controlar el velocímetro y el odómetro, el acople del embrague convertidor de torsión (TCC) transmisiones automáticas,
en algunos se utiliza como señal de referencia de velocidad para el control de crucero y controlar el motoventilador de dos velocidades del radiador.
Tiene en su interior un imán giratorio que genera una onda senoidal de corriente alterna directamente proporcional a la velocidad del vehículo.
Por cada vuelta del eje genera 8 ciclos, su resistencia debe ser de 190 a 240 Ohmios.
Con un voltímetro de corriente alterna se checa el voltaje de salida estando desconectado y poniendo a girar una de las ruedas motrices a unas 40 millas por hora. El voltaje deberá ser 3.2 voltios.
mantenimiento y servicio del ckp
Con un voltímetro de corriente alterna se checa el voltaje de salida estando desconectado y poniendo a girar una de las ruedas motrices a unas 40 millas por hora.
El voltaje deberá ser 3.2 voltios.
Al aparecer éste código, conecte un voltímetro de corriente alterna en sus 2 terminales y ponga a girar la rueda del lado del copiloto.
El voltímetro deberá marcar un voltaje mayor de 1 voltio y se incrementará conforme aumente el giro de la rueda, si esto está bien deberá moverse la aguja del velocímetro, si se mueve, la falla fue intermitente y no está presente.
Si no existe voltaje girando la rueda, revisar el engrane y si éste está bien, quitar el sensor y probarlo afuera haciendo girar el engrane con el voltímetro conectado en sus 2 terminales.
Si no existe voltaje, cambiar el sensor. Puede suceder que tenga el código y las pruebas anteriores sean satisfactorias, entonces borre códigos y pruebe el vehículo. Si después de un recorrido de más de 2 Km. no regresa el código, la falla fue intermitente.
Es necesario un recorrido más largo y si en el recorrido se aprecian variaciones bruscas de la aguja del velocímetro, por lo general es culpa del sensor
Revise el cableado del VSS al ECM antes de cambiar el sensor
Con un voltímetro de corriente alterna se checa el voltaje de salida estando desconectado y poniendo a girar una de las ruedas motrices a unas 40 millas por hora.
El voltaje deberá ser 3.2 voltios.
Al aparecer éste código, conecte un voltímetro de corriente alterna en sus 2 terminales y ponga a girar la rueda del lado del copiloto.
El voltímetro deberá marcar un voltaje mayor de 1 voltio y se incrementará conforme aumente el giro de la rueda, si esto está bien deberá moverse la aguja del velocímetro, si se mueve, la falla fue intermitente y no está presente.
Si no existe voltaje girando la rueda, revisar el engrane y si éste está bien, quitar el sensor y probarlo afuera haciendo girar el engrane con el voltímetro conectado en sus 2 terminales.
Si no existe voltaje, cambiar el sensor. Puede suceder que tenga el código y las pruebas anteriores sean satisfactorias, entonces borre códigos y pruebe el vehículo. Si después de un recorrido de más de 2 Km. no regresa el código, la falla fue intermitente.
Es necesario un recorrido más largo y si en el recorrido se aprecian variaciones bruscas de la aguja del velocímetro, por lo general es culpa del sensor
Revise el cableado del VSS al ECM antes de cambiar el sensor
el nitrox (oxido nitroso)
Se denomina Nitrox a una mezcla gaseosa respirable de oxígeno y nitrógeno utilizada en buceo técnico y recreativo, cuyas proporciones son distintas a las del aire atmosférico: 21% de oxígeno y 79% de nitrógeno aproximadamente.
Nitrox o Aire Enriquecido son términos comúnmente utilizados en buceo para referirese a las mezclas binarias oxígeno-nitrógeno que contienen más oxígeno que el aire atmosférico, es decir, más de 21%. Existen dos mezclas estándares: Nitrox I con 32% de oxígeno y 68% de nitrógeno, y Nitrox II con 36% de oxígeno y 64% de nitrógeno.
Los fundamentos del buceo con mezcla de aire enriquecido o nitrox son los mismos que para el buceo en general (Ver Fundamentos del buceo)
El principal beneficio de bucear con aire enriquecido en oxígeno es la disminución consecuente del contenido de nitrógeno en la botella. Esto permite retardar considerablemente el tiempo de saturación de nitrógeno. Comparado con el aire comprimido estándar, el nitrox usado como mezcla de fondo permite alcanzar mayores tiempos de immersión sin necesidad de realizar paradas dedescompresión. En immersiones de saturación, con paradas de descompresión programadas, el nitrox puede ser empleado como mezcla de tránsito para la descompresión en el ascenso.
Disponener de un completo sistema de carga tanto de aire como de Nitrox garantiza que la mezcla que se respira sea segura y de la mejor calidad. El sistema de carga comienza con un mezclador acoplable a cuaquiera de los compresores donde se realiza la mezcla, esta puede ser aire o bien Nitrox (aire enriquecido con oxígeno) en la proporción deseada. Seguidamente la mezcla es analizada por un oxímetro para garantizar que la carga es la deseada. Una vez hecha, la mezcla pasa a la siguiente etapa del sistema, que se compone de dos compresores independientes donde la mezcla se filtra, se enfria y se deshumidifica. Finalmente la mezcla es introducida en las botellas tras pasar por la rampa de carga. En caso de utilizar Nitrox una vez de cargadas las botellas se espera a que se enfrien y se vuelve a analizar la mezcla con diferentes oxímetros delante del cliente. Tras esta operación se procede al etiquetado de las botellas como corresponde: identificación de la mezcla mediante el porcentaje de oxígeno contenido y máxima profundidad operativa a la presión parcial máxima establecida. Asi ponemos estar seguros de que nuestro nitrox es de 32 % o del 36%
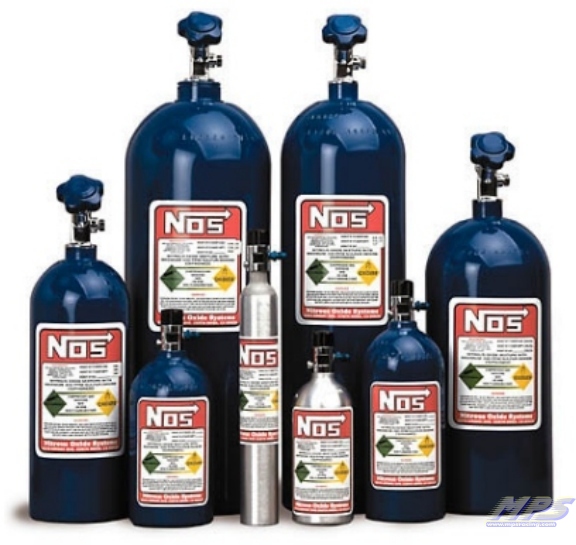
los sensores hall,magnetico,inductivo y optico
La fotoresistencia reduce su resistencia al estar bajo luz.
El fotodiodo conduce en forma inversa al estar bajo luz.
El fototransistor conduce entre emisor y colector en forma directa al estar bajo la luz.
La respuesta de la fotoresistencia es mucho mas lenta que la del fototransistor o de un fotodiodo, es decir responde mas lentamente a variaciones de luz.
Dependiendo de la aplicacion especifica se pueden necesitar componentes opticos y electronicos adicionales: lentes, filtros, amplificador de señal, etc.
A nivel industrial se suele usar sensores opticos "listos" que incluyen circuito electronico, filtros, etc.
En esta pagina de un fabricante aleman de sensores industriales puedes ver mas informacion sobre esos modelos especificos
hall
El sensor de efecto Hall o simplemente sensor Hall o sonda Hall (denominado según Edwin Herbert Hall) se sirve del efecto Hall para la medición de campos magnéticos o corrientes o para la determinación de la posición.
Si fluye corriente por un sensor Hall y se aproxima a un campo magnético que fluye en dirección vertical al sensor, entonces el sensor crea un voltaje saliente proporcional al producto de la fuerza del campo magnético y de la corriente. Si se conoce el valor de la corriente, entonces se puede calcular la fuerza del campo magnético; si se crea el campo magnético por medio de corriente que circula por una bobina o un conductor, entonces se puede medir el valor de la corriente en el conductor o bobina.
Si tanto la fuerza del campo magnético como la corriente son conocidos, entonces se puede usar el sensor Hall como detector de metales.
En la industria del automóvil el sensor Hall se utiliza de forma frecuente, ej. en sensores de posición del cigüeñal (CKP) en el cierre del cinturón de seguridad, en sistemas de cierres de puertas, para el reconocimiento de posición del pedal o del asiento, el cambio de transmisión y para el reconocimiento del momento de arranque del motor. La gran ventaja es la invariabilidad frente a suciedad (no magnética) y agua.
Además puede encontrarse este sensor en circuitos integrados, en impresoras láser donde controlan la sincronización del motor del espejo, en disqueteras de ordenador así como en motores de corriente continua sin escobillas, ej. en ventiladores de PC. Ha llegado a haber incluso teclados con sensores Hall bajo cada tecla.
Los sensores Hall se utilizan en señales salientes análogas para campos magnéticos muy débiles (campo magnético terrestre), ej.brújula en un sistema de navegación.
Como sensores de corriente se usan como bobinas, recorridas con una corriente por medir situadas en la separación del núcleo de hierro. Estos sensores de corriente se comercializan como componentes íntegros, son muy rápidos, se pueden usar para la medición de corrientes continuas (a diferencia de los transformadores de corriente) y proveen una separación de potencial entre circuitos de rendimiento y la electrónica de control.
Como sensor de reconocimiento de posición o tecla a distancia trabajan en conexión con imanes permanentes y disponen de un interruptor de límite integrado.
magnetico
Los sensores de proximidad magnéticos son caracterizados por la posibilidad de distancias grandes de la conmutación, disponible de los sensores con dimensiones pequeñas. Detectan los objetos magnéticos (imanes generalmente permanentes) que se utilizan para accionar el proceso de la conmutación. Los campos magnéticos pueden pasar a través de muchos materiales no magnéticos, el proceso de la conmutación se puede también accionar sin la necesidad de la exposición directa al objeto. Usando los conductores magnéticos (ej. hierro), el campo magnético se puede transmitir sobre mayores distancias para, por ejemplo, poder llevarse la señal de áreas de alta temperatura.
En robótica, algunas situaciones de medición del entorno pueden requerir del uso de elementos de detección sensibles a los campos magnéticos. En principio, si nuestro robot debe moverse en ambientes externos a un laboratorio, una aplicación importante es una brújula que forme parte de un sistema de orientación para nuestro robot. Otra aplicación es la medición directa de campos magnéticos presentes en las inmediaciones, que podrían volverse peligrosos para el "cerebro" de nuestro robot si su intensidad es importante. Una tercera aplicación es la medición de sobrecorrientes en la parte motriz (detectando la intensidad del campo magnético que genera un conductor en la fuente de alimentación). También se podrán encontrar sensores magnéticos en la medición de movimientos, como el uso de detectores de "cero movimiento" y tacómetros basados en sensores por efecto Hall o pickups magnéticos.
inductivo
Los sensores inductivos son una clase especial de sensores que sirven para detectar materiales metálicos ferrosos. Son de gran utilización en la industria, tanto para aplicaciones de posicionamiento como para detectar la presencia o ausencia de objetos metálicos en un determinado contexto: detección de paso, de atasco, de codificación y de conteo.
Los sensores de proximidad inductivos contienen un devanado interno. Cuando una corriente circula por el mismo, un campo magnético es generado, que tiene la dirección de las flechas anaranjadas. Cuando un metal es acercado al campo magnético generado por el sensor de proximidad, éste es detectado

La bobina, o devanado, del sensor inductivo induce corrientes de Foucault en el material por detectar. Estas, a su vez, generan un campo magnético que se opone al de la bobina del sensor, causando una reducción en la inductancia de la misma. Esta reducción en la inductancia de la bobina interna del sensor, trae aparejado una disminución en la impedancia de ésta.
La inductancia es un valor intrínseco de las bobinas o inductores, que depende del diámetro de las espiras y el número de ellas. En sistemas de corriente alterna.
optico
En electronica se utiliza como sensores opticos ciertos componentes sensibles a la luz, en el sentido que modifican su comportamiento electrico segun tengan luz incidente o no.El fotodiodo conduce en forma inversa al estar bajo luz.
El fototransistor conduce entre emisor y colector en forma directa al estar bajo la luz.
La respuesta de la fotoresistencia es mucho mas lenta que la del fototransistor o de un fotodiodo, es decir responde mas lentamente a variaciones de luz.
Dependiendo de la aplicacion especifica se pueden necesitar componentes opticos y electronicos adicionales: lentes, filtros, amplificador de señal, etc.
A nivel industrial se suele usar sensores opticos "listos" que incluyen circuito electronico, filtros, etc.
En esta pagina de un fabricante aleman de sensores industriales puedes ver mas informacion sobre esos modelos especificos
sensor ks (detonacion)

La señal es enviada asì al centro de control, que la procesarà y reconocerà los fenómenos de detonación realizando las correcciones necesarias para regular el encendido del combustible, pudiendo generar un retardo de hasta 10 grados.
Asì este sensor regulará el encendido logrando una mejor combustión lo que brindará al coche más potencia con un consumo menor. Combustibles con un octano mayor permiten que el sistema, en caso de poseer este sensor de detonación, logren un mejor aprovechamiento del combustbile evitando la detonación, manteniendo el avance del encendido. |
Los sensores de detonación son básicamente sensores de vibración y son utilizados para detectar el fenómeno de pistoneo en el motor. El pistoneo ocurre cuando en el motor se produce un fenómeno de combustión no controlada generándose velocidades de frente de llama muy superiores a las normales. El clásico ruido a "pistoneo" que uno suele escuchar (típico cascabeleo) no se trata, como comúnmente se cree, de pistones y aros golpeteando contra el cilindro sino que el ruido que se escucha es el producido por dos frentes de llama que chocan a velocidades y temperaturas muy superiores a las ideales. Por ende la función de este tipo de sensores es la de convertir estas señales acústicas en señales eléctricas para darle aviso a la ECU para que proceda a atrasar la chispa al producirse este fenómeno. El sensor de detonación está compuesto por un elemento toroidal cerámico que al ser comprimido por estas frecuencias de vibración genera una diferencia de potencial entre sus extremos. Esta diferencia de potencial o voltaje generado es el que le informa a la ECU que el fenómeno de pistoneo se esta produciendo.
La estrategia de los distintos sistemas de inyección electrónica es, ante la recepción de señal por parte de este sensor, atrasar la chispa en forma abrupta e ir restituyéndola en forma progresiva hasta volver a los valores de avance de chispa predeterminados para la carga y revoluciones de trabajo. En caso de volverse a recibir señal durante la restitución, el ciclo se repite. Es escencial en estos sensores respetar el par de apriete de fábrica. En caso de estar demasiado apretado a la tapa de cilindros, no podrá captar ninguna señal de detonación y en consecuencia, el motor se la pasara pistoneando sin que la ECU se entere. En caso de que este apretado en defecto, estará permanentemente dando falsas señales de pistoneo y el vehículo estará trabajando permanentemente atrasado.
La estrategia de los distintos sistemas de inyección electrónica es, ante la recepción de señal por parte de este sensor, atrasar la chispa en forma abrupta e ir restituyéndola en forma progresiva hasta volver a los valores de avance de chispa predeterminados para la carga y revoluciones de trabajo. En caso de volverse a recibir señal durante la restitución, el ciclo se repite. Es escencial en estos sensores respetar el par de apriete de fábrica. En caso de estar demasiado apretado a la tapa de cilindros, no podrá captar ninguna señal de detonación y en consecuencia, el motor se la pasara pistoneando sin que la ECU se entere. En caso de que este apretado en defecto, estará permanentemente dando falsas señales de pistoneo y el vehículo estará trabajando permanentemente atrasado.
sensor maf
En algunos sesnores MAF la señal entregada es una corriente pulsante de frecuencia variable ( En algunos modelos de GM, por ejemplo).
El senor MAF mayormente difundido es el el llamado Sensor MAF por hilo caliente.
En este sensor, internamente funciona mediante un hilo muy fino metálico el cual se encuentra a muy alta temperatura, en el momento que comienza a entrar aire el aire enfría este hilo y las cargas cambiantes de aire causan un efecto diferente sobre la temperatura del hilo, entonces todo el circuito que maneja el tema del calentamiento del hilo generara una señal de voltaje de acuerdo a que tanto es enfriado.
Esto se encuentra incorporado dentro del sensor, el cual va ubicado en el sistema de admisión del vehículo, lo más próximo al filtro de aire del motor.
Internamente existe un circuito que permanente monitorea los cambios de temperatura del hilo por medio de un transductor eléctrico, esto dentro del sensor.
Es importante interpretar que el MAF es un conjunto sellado y de este dispositivo sale una señal hacia el PCM, que es la que realmente nos interesa al momento de la medición o verificación.
Entonces será necesario controlar que por el cable de señal se este generando un valor de voltaje de acuerdo al volumen del aire que ingresa al motor bajo distintas condiciones de carga.
En esta imagen se puede apreciar claramente que el cable del multimetro o el osciloscopio debe estar ubicado en la salida del sensor.
El cable negativo debe estar dispuesto en la masa del motor. Uuna vez realizada esta operación se procede a cambiar cargas en el motor y de acuerdo a esto se debe registrar un cambio de voltaje en la herramienta de medición. Los datos precisos de voltaje que debe contener cada condición del motor no siempre están descritos en el manual del fabricante. Por este motivo resulta particularmente interesante construir tablas de control del MAF.
valvula iac
IAC SIGNIFICA IDLE AIR CONTROL, (CONTROL DE MARCHA MINIMA) Y ES UN COMPONENTE DE LOS MOTORES CON INYECCION ELECTRONICA QUE SE ENCARGA DE REGULAR LA MARCHA MINIMA DEL MOTOR, O RALENTI, ESTA TRABAJA POR MEDIO DE SEÑALES ELECTRICAS QUE ENVIA LA COMPUTADORA DEL MOTOR DEPENDIENDO DE LOS DIFERENTES ESTADOS DE FUNCIONAMIENTO CUANDO EL ACELERADOR NO SE ESTA PISANDO.
POR EJ. CUANDO ARRANCAS EL MOTOR ESTE SE ACELERA LIGERAMENTE Y LUEGO SE ESTABILIZA GRACIAS A LA "IAC", O CUANDO PONES VELOCIDAD EN UN AUTO AUTOMATICO ESTA VALVULA ACELERA UN POCO EL MOTOR PARA EVITAR QUE SE APAGUE Y ESTABILIZA LAS REVOLUCIONES RPM. TAMBIEN AL PONER EL AIRE ACONDICIONADO EL MOTOR TIENDE A BAJAR DE REVOLUCIONES Y LA IAC LO ESTABILIZA.
ES IMPORTANTE DAR MANTENIMENTO "LIMPIEZA Y LUBRICACION " A ESTA VALVULA YA QUE SI SE SATURA DE CARBON O DE SUCIEDAD PRODUCIDA POR LOS GASES DE ACEITE DEL MOTOR, ESTA SE ATORA Y PUEDE DAR PROBLEMAS COMO ACELERACION EXCESIVA EN MARCHA MINIMA O QUE EL MOTOR SE APAGUE.
LA IAC ES UN PEQUEÑO MOTOR ELECTORMAGNETICO QUE TRABAJA CON DOBLE POLARIDAD ES DECIR EN DOS DIRECCIONES Y ESO LE PERMITE DEJAR PASAR MAS AIRE O MENOS AIRE AL MULTIPLE DE ADMISION PARA CALIBRAR LA MEZCLA AIRE COMBUSTIBLE. ESTO SIEMPRE EN MARCHA MINIMA. UNA VEZ QUE TU ACELERAS EL MOTOR O PISAS EL ACELERADOR, LA FUNCION DE ESTA VALVULA YA NO ES TRASCENDENTE, SU FUNCION SOLO ES IMPORTANTE EN MARCHA MINIMA.
TAMBIEN SE LE CONOCE COMO MOTOR "AIS" O VALVULA "BY PASS" PERO LA FUNCION ES LA MISMA
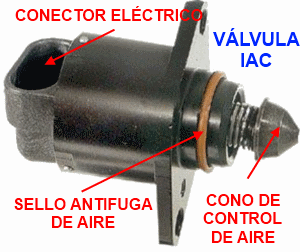
IAC SIGNIFICA IDLE AIR CONTROL, (CONTROL DE MARCHA MINIMA) Y ES UN COMPONENTE DE LOS MOTORES CON INYECCION ELECTRONICA QUE SE ENCARGA DE REGULAR LA MARCHA MINIMA DEL MOTOR, O RALENTI, ESTA TRABAJA POR MEDIO DE SEÑALES ELECTRICAS QUE ENVIA LA COMPUTADORA DEL MOTOR DEPENDIENDO DE LOS DIFERENTES ESTADOS DE FUNCIONAMIENTO CUANDO EL ACELERADOR NO SE ESTA PISANDO.
POR EJ. CUANDO ARRANCAS EL MOTOR ESTE SE ACELERA LIGERAMENTE Y LUEGO SE ESTABILIZA GRACIAS A LA "IAC", O CUANDO PONES VELOCIDAD EN UN AUTO AUTOMATICO ESTA VALVULA ACELERA UN POCO EL MOTOR PARA EVITAR QUE SE APAGUE Y ESTABILIZA LAS REVOLUCIONES RPM. TAMBIEN AL PONER EL AIRE ACONDICIONADO EL MOTOR TIENDE A BAJAR DE REVOLUCIONES Y LA IAC LO ESTABILIZA.
ES IMPORTANTE DAR MANTENIMENTO "LIMPIEZA Y LUBRICACION " A ESTA VALVULA YA QUE SI SE SATURA DE CARBON O DE SUCIEDAD PRODUCIDA POR LOS GASES DE ACEITE DEL MOTOR, ESTA SE ATORA Y PUEDE DAR PROBLEMAS COMO ACELERACION EXCESIVA EN MARCHA MINIMA O QUE EL MOTOR SE APAGUE.
LA IAC ES UN PEQUEÑO MOTOR ELECTORMAGNETICO QUE TRABAJA CON DOBLE POLARIDAD ES DECIR EN DOS DIRECCIONES Y ESO LE PERMITE DEJAR PASAR MAS AIRE O MENOS AIRE AL MULTIPLE DE ADMISION PARA CALIBRAR LA MEZCLA AIRE COMBUSTIBLE. ESTO SIEMPRE EN MARCHA MINIMA. UNA VEZ QUE TU ACELERAS EL MOTOR O PISAS EL ACELERADOR, LA FUNCION DE ESTA VALVULA YA NO ES TRASCENDENTE, SU FUNCION SOLO ES IMPORTANTE EN MARCHA MINIMA.
TAMBIEN SE LE CONOCE COMO MOTOR "AIS" O VALVULA "BY PASS" PERO LA FUNCION ES LA MISMA
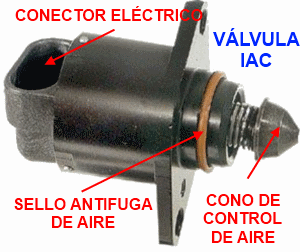
sensor de mariposa
El TPS monitorea la abertura de la mariposa de aceleración y con esta información la computadora realiza ajustes en la mezcla aire-combustible.
Recibe 5 Voltios de alimentación de la computadora.
El TPS envía una señal a la computadora. Señal que va desde .5 Voltios en marcha mínima (o papalote de aceleración completamente cerrado), hasta 4.8 Voltios con el papalote de aceleración completamente abierto.
Se puede probar con un multimetro con el motor apagado y el switch "abierto" (en posición ON).
Conectando la terminal roja del multimetro en el cable de enmedio del conector del TPS. (tiene 3 cables), que es el que envía la señal a la computadora. Y la terminal negra en tierra.
Debe marcar entre .5 hasta 1 Voltio con el sw abierto y la mariposa cerrada, abrela suavemente, y conforme la vas abriendo (acelerando) el voltaje se va incrementendo, hasta legar a 3.8 - 4.8 V, dependiendo del vehiculo.
Los sintomas de falla son:
Marcha mínima variable
Hay titubeo y ahogamiento durante la aceleración o desaceleración.
Hay bajo rendimiento del motor (mayor consumo de gasolina)
Ojo: antes de cambiarel sensor TPS,o hay que checar si esta bien conectado, si el conector no esta sucio o corroido, si algun cable esta roto, etc.
El TPS monitorea la abertura de la mariposa de aceleración y con esta información la computadora realiza ajustes en la mezcla aire-combustible.
Recibe 5 Voltios de alimentación de la computadora.
El TPS envía una señal a la computadora. Señal que va desde .5 Voltios en marcha mínima (o papalote de aceleración completamente cerrado), hasta 4.8 Voltios con el papalote de aceleración completamente abierto.
Se puede probar con un multimetro con el motor apagado y el switch "abierto" (en posición ON).
Conectando la terminal roja del multimetro en el cable de enmedio del conector del TPS. (tiene 3 cables), que es el que envía la señal a la computadora. Y la terminal negra en tierra.
Debe marcar entre .5 hasta 1 Voltio con el sw abierto y la mariposa cerrada, abrela suavemente, y conforme la vas abriendo (acelerando) el voltaje se va incrementendo, hasta legar a 3.8 - 4.8 V, dependiendo del vehiculo.
Los sintomas de falla son:
Marcha mínima variable
Hay titubeo y ahogamiento durante la aceleración o desaceleración.
Hay bajo rendimiento del motor (mayor consumo de gasolina)
Ojo: antes de cambiarel sensor TPS,o hay que checar si esta bien conectado, si el conector no esta sucio o corroido, si algun cable esta roto, etc.
resumen de los diodos
En este trabajo se pretende realizar un resumen acerca algunos de los tipos de diodos existentes,
encuanto a sus características, su principio de funcionamiento, sus modos de conexion mas comunes y
las aplicaciones de los diodos mas usados en electronica como el caso de los diodos Varicap, Zener,
LED, el Diodo Schottky, diodo Tunel, los fotodiodos etc..
Un diodo (del griego "dos caminos") es un dispositivo semiconductor que permite el paso de la
corriente eléctrica en una única dirección con características similares a un interruptor. De forma
simplificada, la curva característica de un diodo (I-V) consta de dos regiones: por debajo de cierta
diferencia de potencial, se comporta como un circuito abierto (no conduce), y por encima de ella como
un corto circuito con muy pequeña resistencia eléctrica.
Debido a este comportamiento, se les suele denominar rectificadores, ya que son dispositivos capaces
de convertir una corriente alterna en corriente continua. Su principio de funcionamiento está basado en
los experimentos de Lee De Forest.
Los primeros diodos eran válvulas grandes en chips o tubos de vacío, también llamadas válvulas
termoiónicas constituidas por dos electrodos rodeados de vacío en un tubo de cristal, con un aspecto
similar al de las lámparas incandescentes. El invento fue realizado en 1904 por John Ambrose Fleming,
de la empresa Marconi, basándose en observaciones realizadas por Thomas Alva Edison.- Al igual que
las lámparas incandescentes, los tubos de vacío tienen un filamento (el cátodo) a través del que circula
la corriente, calentándolo por efecto Joule. El filamento está tratado con óxido de bario, de modo que al
calentarse emite electrones al vacío circundante; electrones que son conducidos electrostáticamente
hacia una placa característica corvada por un muelle doble cargada positivamente (el ánodo),
produciéndose así la conducción. Evidentemente, si el cátodo no se calienta, no podrá ceder electrones.
Por esa razón los circuitos que utilizaban válvulas de vacío requerían un tiempo para que las válvulas
se calentaran antes de poder funcionar y las válvulas se quemaban con mucha facilidad.
En este trabajo se pretende realizar un resumen acerca algunos de los tipos de diodos existentes,
encuanto a sus características, su principio de funcionamiento, sus modos de conexion mas comunes y
las aplicaciones de los diodos mas usados en electronica como el caso de los diodos Varicap, Zener,
LED, el Diodo Schottky, diodo Tunel, los fotodiodos etc..
Un diodo (del griego "dos caminos") es un dispositivo semiconductor que permite el paso de la
corriente eléctrica en una única dirección con características similares a un interruptor. De forma
simplificada, la curva característica de un diodo (I-V) consta de dos regiones: por debajo de cierta
diferencia de potencial, se comporta como un circuito abierto (no conduce), y por encima de ella como
un corto circuito con muy pequeña resistencia eléctrica.
Debido a este comportamiento, se les suele denominar rectificadores, ya que son dispositivos capaces
de convertir una corriente alterna en corriente continua. Su principio de funcionamiento está basado en
los experimentos de Lee De Forest.
Los primeros diodos eran válvulas grandes en chips o tubos de vacío, también llamadas válvulas
termoiónicas constituidas por dos electrodos rodeados de vacío en un tubo de cristal, con un aspecto
similar al de las lámparas incandescentes. El invento fue realizado en 1904 por John Ambrose Fleming,
de la empresa Marconi, basándose en observaciones realizadas por Thomas Alva Edison.- Al igual que
las lámparas incandescentes, los tubos de vacío tienen un filamento (el cátodo) a través del que circula
la corriente, calentándolo por efecto Joule. El filamento está tratado con óxido de bario, de modo que al
calentarse emite electrones al vacío circundante; electrones que son conducidos electrostáticamente
hacia una placa característica corvada por un muelle doble cargada positivamente (el ánodo),
produciéndose así la conducción. Evidentemente, si el cátodo no se calienta, no podrá ceder electrones.
Por esa razón los circuitos que utilizaban válvulas de vacío requerían un tiempo para que las válvulas
se calentaran antes de poder funcionar y las válvulas se quemaban con mucha facilidad.

cuanto aire y combustible entra en la mezcla
Para que el motor de gasolina funcione adecuadamente, debe prepararse la mezcla de aire y combustible de manera adecuada. Esta mezcla comienza a formarse desde el punto donde se unen gasolina y aire, continua por el conducto de admisión, luego durante la carrera de admisión del pistón y termina durante la carrera de compresión, en la cual el calentamiento del aire debido al incremento de la presión (los gases se calientan cuando se comprimen) evapora la gasolina y la mezcla íntimamente con el aire.
Químicamente hablando, existe una cantidad exacta de aire (que proporciona el oxigeno) para hacer la combustión de la gasolina sin que sobre ni aire ni combustible, esta cantidad se llama relación estequeométrica, y para las gasolinas comerciales, está entre 14 y 15 veces la cantidad de aire en peso, por la cantidad de gasolina, pero en la práctica, en el motor real no puede usarse esa relación porque parte del combustible saldría por el escape sin quemar, debido al escaso tiempo que tienen para encontrarse y reaccionar los miles de millones de moléculas de oxígeno, con las otras tantas de combustible. Ilustremos la situación de la combustión dentro del cilindro con el ejemplo siguiente.
Supongamos que vamos a un gran baile con 5000 mujeres (combustible), y 5000 hombres (aire), y que este; solo dure unos 30 minutos, la posibilidad de que todas las mujeres encuentren un hombre con quien bailar, es muy remota, y lo mas probable es que se acabe el baile, y todavía queden parejas sin formarse, no obstante, si la cantidad de hombres es mayor que la de mujeres, la probabilidad de que las féminas no encuentren pareja es mucho menor, aunque sobren hombres que no bailarán con nadie. Del mismo modo se hace en el motor de combustión interna, se introduce al cilindro mas aire del estequeométricamente necesario, para garantizar el quemado total del combustible cuando se quiere obtener gases de escape limpios de combustible sin quemar.
Esta cantidad de exceso de aire no puede ser indiscriminada, ya que si es demasiado grande, parte de la energía de la gasolina se gasta calentando el aire sobrante, que luego es desechada por el escape reduciendo la potencia y eficiencia del motor, de manera que hay un óptimo que los dispositivos de preparación de la mezcla tratan de seguir lo mejor posible.
De acuerdo a los requerimientos a que se destine el motor.
Para que el motor de gasolina funcione adecuadamente, debe prepararse la mezcla de aire y combustible de manera adecuada. Esta mezcla comienza a formarse desde el punto donde se unen gasolina y aire, continua por el conducto de admisión, luego durante la carrera de admisión del pistón y termina durante la carrera de compresión, en la cual el calentamiento del aire debido al incremento de la presión (los gases se calientan cuando se comprimen) evapora la gasolina y la mezcla íntimamente con el aire.
Químicamente hablando, existe una cantidad exacta de aire (que proporciona el oxigeno) para hacer la combustión de la gasolina sin que sobre ni aire ni combustible, esta cantidad se llama relación estequeométrica, y para las gasolinas comerciales, está entre 14 y 15 veces la cantidad de aire en peso, por la cantidad de gasolina, pero en la práctica, en el motor real no puede usarse esa relación porque parte del combustible saldría por el escape sin quemar, debido al escaso tiempo que tienen para encontrarse y reaccionar los miles de millones de moléculas de oxígeno, con las otras tantas de combustible. Ilustremos la situación de la combustión dentro del cilindro con el ejemplo siguiente.
Supongamos que vamos a un gran baile con 5000 mujeres (combustible), y 5000 hombres (aire), y que este; solo dure unos 30 minutos, la posibilidad de que todas las mujeres encuentren un hombre con quien bailar, es muy remota, y lo mas probable es que se acabe el baile, y todavía queden parejas sin formarse, no obstante, si la cantidad de hombres es mayor que la de mujeres, la probabilidad de que las féminas no encuentren pareja es mucho menor, aunque sobren hombres que no bailarán con nadie. Del mismo modo se hace en el motor de combustión interna, se introduce al cilindro mas aire del estequeométricamente necesario, para garantizar el quemado total del combustible cuando se quiere obtener gases de escape limpios de combustible sin quemar.
Esta cantidad de exceso de aire no puede ser indiscriminada, ya que si es demasiado grande, parte de la energía de la gasolina se gasta calentando el aire sobrante, que luego es desechada por el escape reduciendo la potencia y eficiencia del motor, de manera que hay un óptimo que los dispositivos de preparación de la mezcla tratan de seguir lo mejor posible.
De acuerdo a los requerimientos a que se destine el motor.
sensor de oxigeno
La sonda lambda (Sonda-λ), es un sensor que está situado en el conducto de escape, inmediatamente antes del catalizador, de forma que puede medir la concentración de oxígeno en los gases de escape antes de que sufran alguna alteración. La medida del oxígeno es representativa del grado de riqueza de la mezcla, magnitud que la sonda transforma en un valor de tensión y que comunica a la unidad de control del motor.
Los gases de escape de un motor de ciclo Otto están formados en un 80% por Nitrógeno, que no participa prácticamente en la reacción química de combustión, un 14-16% de dióxido de carbono o CO2, y el resto agua (vapor) además de una pequeña proporción de contaminantes, siendo los principales los hidrocarburos (HC) y el monóxido de carbono (CO) . El oxígeno residual es de un 0,3 % aproximadamente. Su proporción varía bastante en función del factor lambda.
La sonda en sí está constituida por una parte cerámica y unos electrodos de platino. Los gases de escape están en contacto con la sonda y esta toma información de la proporción de oxígeno residual tras la combustión.
La sonda lambda (Sonda-λ), es un sensor que está situado en el conducto de escape, inmediatamente antes del catalizador, de forma que puede medir la concentración de oxígeno en los gases de escape antes de que sufran alguna alteración. La medida del oxígeno es representativa del grado de riqueza de la mezcla, magnitud que la sonda transforma en un valor de tensión y que comunica a la unidad de control del motor.
Los gases de escape de un motor de ciclo Otto están formados en un 80% por Nitrógeno, que no participa prácticamente en la reacción química de combustión, un 14-16% de dióxido de carbono o CO2, y el resto agua (vapor) además de una pequeña proporción de contaminantes, siendo los principales los hidrocarburos (HC) y el monóxido de carbono (CO) . El oxígeno residual es de un 0,3 % aproximadamente. Su proporción varía bastante en función del factor lambda.
La sonda en sí está constituida por una parte cerámica y unos electrodos de platino. Los gases de escape están en contacto con la sonda y esta toma información de la proporción de oxígeno residual tras la combustión.
Esa información se transmite a la central de la inyección electrónica y así esta central puede regular la cantidad de combustible que inyecta en el cilindro para mantener la relación lo más próxima a 1/14,7 llamada relación estequiométrica.
La medición se basa en la cantidad de oxígeno restante en el gas evacuado por el tubo de escape. La sonda lambda es uno de los sensores de corrección principales en la electrónica de control, conocido como regulación de lambda para la limpieza catalítica del gas emitido (popularmente denominado catalizador regulado). El sensor se basa en dos principios diferentes para las mediciones: el voltaje de un electrolito (sonda de Walther Nernst) y una variación de la resistencia eléctrica de una resistencia de cerámica (sonda de resistencia).
Su campo principal de aplicación es el motor de combustión interna, de ciclo Otto principalmente de inyección de combustible, pero también se usa para regular el gas emitido por calderas de condensación y motores diésel.

conexion tipo puente
Un Puente H o Puente en H es un circuito electrónico que permite a un motor eléctrico DC girar en ambos sentidos, avance yretroceso. Son ampliamente usados en robótica y como convertidores de potencia. Los puentes H están disponibles como circuitos integrados, pero también pueden construirse a partir de componentes discreto.
Con la nomenclatura que estamos usando, los interruptores S1 y S2 nunca podrán estar cerrados al mismo tiempo, porque esto cortocircuitaría la fuente de tensión. Lo mismo sucede con S3 y S4.El término "puente H" proviene de la típica representación gráfica del circuito. Un puente H se construye con 4 interruptores (mecánicos o mediante transistores). Cuando los interruptores S1 y S4 (ver primera figura) están cerrados (y S2 y S3 abiertos) se aplica una tensión positiva en el motor, haciéndolo girar en un sentido. Abriendo los interruptores S1 y S4 (y cerrando S2 y S3), el voltaje se invierte, permitiendo el giro en sentido inverso del motor.
Como hemos dicho el puente H se usa para invertir el giro de un motor, pero también puede usarse para frenarlo (de manera brusca), al hacer un corto entre las bornas del motor, o incluso puede usarse para permitir que el motor frene bajo su propia inercia, cuando desconectamos el motor de la fuente que lo alimenta
el sensor de temperatura
El bulbo sensor de temperatura, o también denominado bulbo remoto, de las válvulas de expansión termostáticas y válvulas limitadoras de presión es el elemento que mide el grado de sobrecalentamiento del vapor de refrigerante a la salida del evaporador.
Este bulbo, el que está conectado a la parte superior de la válvula por medio de un tubo capilar, se encuentra lleno de un fluido potencia denominado carga termostática, el cual al evaporarse ejerce una fuerza sobre el diafragma de la válvula controlando el flujo de refrigerante al interior del evaporador.
El funcionamiento adecuado de la válvula depende de la localización e instalación del bulbo. Ya que generalmente se usa un bulbo instalado en el exterior de la tubería –debido a que existen otros que también puede ir dentro de ella- este debe ir firmemente fijado con abrazaderas metálicas y cercano a la salida del evaporador, en posición horizontal. Su ángulo de fijación está recomendado a 45º por debajo del plano horizontal; si la tubería es demasiado estrecha o de igual sección circular que la del bulbo, se recomienda montar el bulbo sobre esta. Todo este artificio es necesario a fin de evitar las erróneas señales de temperatura que arroja el aceite alojado en la parte inferior de la tubería a la salida del evaporador, las cuales indican un equívoco valor de sobrecalentamiento, distinto al del vapor de refrigerante.
sistema de encendidos (bobina,platino,condensador y DIS)
bobina
La bobina del encendido es un dispositivo de inducción electromagnética o inductor, que forma parte del encendido de unos motor de combustión interna alternativo de ciclo Otto oWankel, que cumple con la función de elevar el voltaje normal de a bordo (6, 12 o 24 V, según los casos) en un valor unas 1000 veces mayor con objeto de lograr el arco eléctrico o chispa en la bujía, para permitir la inflamación de la mezcla aire/combustible en la cámara de combustión.
Consta de dos arrollamientos, primario y secundario, con una relación de espiras de 1 a 1000 aproximadamente, con grosores inversamente proporcionales a dichas longitudes, y un núcleo ferromagnético. Cuenta con dos conexiones para el primario: una de alimentación positiva desde el contacto de encendido del motor, y una de negativo al dispositivo de interrupción cíclica del primario. El secundario cuenta con una conexión a masa, y otra de salida de alta tensión hacia la bujía o en su caso hacia el distribuidor.La interrupción cíclica del primario está sincronizada con el motor, una vez cada giro en el dos tiempos (2T) o una cada dos giros en el cuatro tiempos (4T); aunque existen sistemas de 4T en motores de más de un cilindro, con chispa en cada revolución (Sistema de chispa perdida o DIS) Dicha interrupción era antiguamente mecánica gracias al ruptor o platinos, y hoy día se realiza mediante un circuito electrónico, siendo un transistor de potencia que depende de un controlador asociado al régimen del motor gracias a un sensorde régimen .
La interrupción cíclica del primario está sincronizada con el motor, una vez cada giro en el dos tiempos (2T) o una cada dos giros en el cuatro tiempos (4T); aunque existen sistemas de 4T en motores de más de un cilindro, con chispa en cada revolución (Sistema de chispa perdida o DIS) Dicha interrupción era antiguamente mecánica gracias al ruptor o platinos, y hoy día se realiza mediante un circuito electrónico, siendo un transistor de potencia que depende de un controlador asociado al régimen del motor gracias a un sensorde régimen .

platinos
Sistema de encendido por platinos. Fallas más comunes.
Las fallas que mencionas, no están relacionadas con el sistema de encendido por platinos.
Los componentes del encendido por platinos, es el distribuidor, el condensador, obvio el platino, la bobina, los cables y las bujías.
La falla mas común presentan regularmente es que los platinos se "flamean" ya sea por un desgaste de los mismos, porque el condensador (el condensador no es mas que una resistencia) este inservible, o por una mala calibración, esto provoca que el motor aviente explosiones por el escape, que cueste trabajo arrancarlo, que la maquina se escuche dispareja, que el auto se de de jalones, etc.
Este sistema de encendido por platinos, (a comparacion del encendido electrónico), presenta un desgaste físico, causado por el roce entre la leva que abre el platino y el mismo platino, y esto causa que el platino se descalibre, igualmente en ocaciones el porta-platinos presenta un movimiento excesivo, e igualmente causa que el platino se mueva, y no abra correctamente a la medida.
El motor de arranque es a lo que le llaman "marcha" sirve para hacer girar el motor para que comience a llevar a cabo las combustiones.
Los bujes son un tipo de rodamientos, para evitar la fricción metal con metal, y los rodamientos pueden ser, como ya mencione, bujes o también pueden ser baleros. pero ni el motor de arranque ni los rodamientos están relacionados con el sistema de platinos, puesto que el sistema de platinos es el "sistema de ignición".
SISTEMA DE ENCENDIDO: El equipo de encendido enciende la mezcla de aire-combustible la cual es comprimida en el interior del cilindro. EI equipo de encendido es requerido para generar suficiente chispa para encender la mezcla de aire-combustible y para generar estas chispas con la distribución que corresponde a la condición de funcionamiento del motor, también que sea extremadamente durable.
COMPONENTES DEL SISTEMA DE ENCENDIDO
Bobina de Encendido: Este dispositivo.

condensador
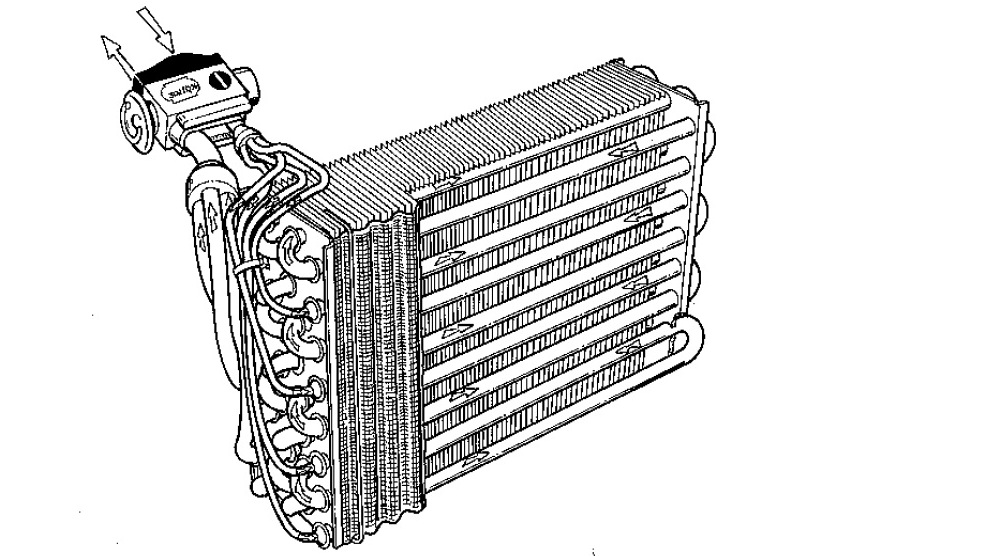
DIS
El sistema de encendido DIS (Direct Ignition System) tambien llamado sistema de encendido sin distribuidor (Distributorless Ignition System), se diferencia del sistema de encendido tradicional en suprimir el distribuidor, con esto se consigue eliminar los elementos mecánicos, siempre propensos a sufrir desgastes y averías.
Las ventajas del sistema DIS frente al sistema convencional son las siguientes:
Mayor tiempo para que la bobina genere el suficiente campo magnético para hacer saltar la chispa que inflame la mezcla, lo que reduce el numero de fallos de encendido a altas revoluciones en los cilindros por no ser suficiente la calidad de la chispa que impide inflamar la mezcla.
Menor interferencias eléctricas del distribuidor por lo que se mejora la fiabilidad del funcionamiento del motor, las bobinas pueden ser colocadas cerca de las bujías con lo que se reduce la longitud de los cables de alta tensión, incluso se llegan a eliminar estos en algunos casos como ya veremos.
bobina
La bobina del encendido es un dispositivo de inducción electromagnética o inductor, que forma parte del encendido de unos motor de combustión interna alternativo de ciclo Otto oWankel, que cumple con la función de elevar el voltaje normal de a bordo (6, 12 o 24 V, según los casos) en un valor unas 1000 veces mayor con objeto de lograr el arco eléctrico o chispa en la bujía, para permitir la inflamación de la mezcla aire/combustible en la cámara de combustión.
Consta de dos arrollamientos, primario y secundario, con una relación de espiras de 1 a 1000 aproximadamente, con grosores inversamente proporcionales a dichas longitudes, y un núcleo ferromagnético. Cuenta con dos conexiones para el primario: una de alimentación positiva desde el contacto de encendido del motor, y una de negativo al dispositivo de interrupción cíclica del primario. El secundario cuenta con una conexión a masa, y otra de salida de alta tensión hacia la bujía o en su caso hacia el distribuidor.La interrupción cíclica del primario está sincronizada con el motor, una vez cada giro en el dos tiempos (2T) o una cada dos giros en el cuatro tiempos (4T); aunque existen sistemas de 4T en motores de más de un cilindro, con chispa en cada revolución (Sistema de chispa perdida o DIS) Dicha interrupción era antiguamente mecánica gracias al ruptor o platinos, y hoy día se realiza mediante un circuito electrónico, siendo un transistor de potencia que depende de un controlador asociado al régimen del motor gracias a un sensorde régimen .
La interrupción cíclica del primario está sincronizada con el motor, una vez cada giro en el dos tiempos (2T) o una cada dos giros en el cuatro tiempos (4T); aunque existen sistemas de 4T en motores de más de un cilindro, con chispa en cada revolución (Sistema de chispa perdida o DIS) Dicha interrupción era antiguamente mecánica gracias al ruptor o platinos, y hoy día se realiza mediante un circuito electrónico, siendo un transistor de potencia que depende de un controlador asociado al régimen del motor gracias a un sensorde régimen .

platinos
Sistema de encendido por platinos. Fallas más comunes.
Las fallas que mencionas, no están relacionadas con el sistema de encendido por platinos.
Los componentes del encendido por platinos, es el distribuidor, el condensador, obvio el platino, la bobina, los cables y las bujías.
La falla mas común presentan regularmente es que los platinos se "flamean" ya sea por un desgaste de los mismos, porque el condensador (el condensador no es mas que una resistencia) este inservible, o por una mala calibración, esto provoca que el motor aviente explosiones por el escape, que cueste trabajo arrancarlo, que la maquina se escuche dispareja, que el auto se de de jalones, etc.
Este sistema de encendido por platinos, (a comparacion del encendido electrónico), presenta un desgaste físico, causado por el roce entre la leva que abre el platino y el mismo platino, y esto causa que el platino se descalibre, igualmente en ocaciones el porta-platinos presenta un movimiento excesivo, e igualmente causa que el platino se mueva, y no abra correctamente a la medida.
El motor de arranque es a lo que le llaman "marcha" sirve para hacer girar el motor para que comience a llevar a cabo las combustiones.
Los bujes son un tipo de rodamientos, para evitar la fricción metal con metal, y los rodamientos pueden ser, como ya mencione, bujes o también pueden ser baleros. pero ni el motor de arranque ni los rodamientos están relacionados con el sistema de platinos, puesto que el sistema de platinos es el "sistema de ignición".
SISTEMA DE ENCENDIDO: El equipo de encendido enciende la mezcla de aire-combustible la cual es comprimida en el interior del cilindro. EI equipo de encendido es requerido para generar suficiente chispa para encender la mezcla de aire-combustible y para generar estas chispas con la distribución que corresponde a la condición de funcionamiento del motor, también que sea extremadamente durable.
COMPONENTES DEL SISTEMA DE ENCENDIDO
Bobina de Encendido: Este dispositivo.

condensador
Este sistema llamado también "encendido por tiristor" funciona de una manera distinta a todos los sistemas de encendido (encendido por bobina) tratados hasta aquí . Su funcionamiento se basa en cargar un condensador con energía eléctrica para luego descargarlo provocando en este momento la alta tensión que hace saltar la chispa en las bujías.
En el encendido por bobina, el tiempo de crecimiento de la tensión secundaria y la duración de la chispa son relativamente largos (del orden de 0,1 milisegundo y 1 msg respectivamente), no permitiendo su aplicación en motores de alto régimen de funcionamiento sobre todo en aquellos en los que el numero de cilindros es elevado. Para motores de carácter deportivo donde es necesario almacenar una gran cantidad de energía eléctrica para después descargarla en las bujías en intervalos muy cortos de tiempo por el elevado numero de revoluciones a la que funcionan estos motores, se utiliza el encendido por descarga de condensador.
En el encendido por bobina, el tiempo de crecimiento de la tensión secundaria y la duración de la chispa son relativamente largos (del orden de 0,1 milisegundo y 1 msg respectivamente), no permitiendo su aplicación en motores de alto régimen de funcionamiento sobre todo en aquellos en los que el numero de cilindros es elevado. Para motores de carácter deportivo donde es necesario almacenar una gran cantidad de energía eléctrica para después descargarla en las bujías en intervalos muy cortos de tiempo por el elevado numero de revoluciones a la que funcionan estos motores, se utiliza el encendido por descarga de condensador.
En este tipo de encendido, la energía es almacenada en un condensador de capacidad "C", cargado a la tensión "V". El valor de la capacidad del condensador esta limitada a 1 o 2 microFaradios debido a evidentes razones de dimensión del condensador, intentando aumentar el nivel de energía almacenada aplicando tensiones elevadas. En la practica se utilizan valores de tensión alrededor de los 400 V. Por lo tanto es necesario disponer de un sistema que permita elevar la tensión de la batería para obtener los valores de tensión indicados (400 V).
Cuando el alternador esta cargado, la descarga se realiza muy rápidamente a través del arrollamiento primario del transformador de encendido, elevando la tensión del condensador al valor de la alta tensión necesaria en el secundario, con el fin de provocar la chispa en la bujía, como en el caso de encendido por bobinado inductivo.El transformador de encendido (2): el transformador utilizado en este tipo de encendido se asemeja a la bobina del encendido inductivo solo en la forma exterior, ya que en su construcción interna varia, en su funcionamiento es un transformador de impulsos que convierte la corriente de carga rápida del condensador, a través de su bobinado primario en una alta tensión que aparecerá rápidamente en el bobinado secundario. A pesar de que el transformador tiene el aspecto de una bobina tradicional, su concepción eléctrica es bien distinta ya que su inductancia primaria es muy inferior y por consiguiente el circuito de descarga del condensador tendrá una impedancia global pequeña, permitiendo una rápida elevación de la tensión.
Cuando el alternador esta cargado, la descarga se realiza muy rápidamente a través del arrollamiento primario del transformador de encendido, elevando la tensión del condensador al valor de la alta tensión necesaria en el secundario, con el fin de provocar la chispa en la bujía, como en el caso de encendido por bobinado inductivo.El transformador de encendido (2): el transformador utilizado en este tipo de encendido se asemeja a la bobina del encendido inductivo solo en la forma exterior, ya que en su construcción interna varia, en su funcionamiento es un transformador de impulsos que convierte la corriente de carga rápida del condensador, a través de su bobinado primario en una alta tensión que aparecerá rápidamente en el bobinado secundario. A pesar de que el transformador tiene el aspecto de una bobina tradicional, su concepción eléctrica es bien distinta ya que su inductancia primaria es muy inferior y por consiguiente el circuito de descarga del condensador tendrá una impedancia global pequeña, permitiendo una rápida elevación de la tensión.
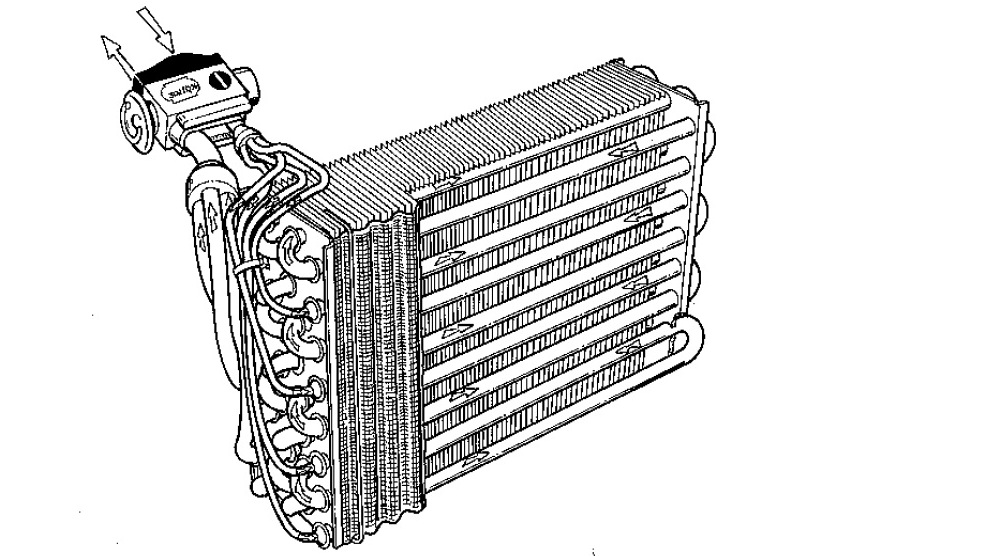
DIS
El sistema de encendido DIS (Direct Ignition System) tambien llamado sistema de encendido sin distribuidor (Distributorless Ignition System), se diferencia del sistema de encendido tradicional en suprimir el distribuidor, con esto se consigue eliminar los elementos mecánicos, siempre propensos a sufrir desgastes y averías.
Las ventajas del sistema DIS frente al sistema convencional son las siguientes:
Mayor tiempo para que la bobina genere el suficiente campo magnético para hacer saltar la chispa que inflame la mezcla, lo que reduce el numero de fallos de encendido a altas revoluciones en los cilindros por no ser suficiente la calidad de la chispa que impide inflamar la mezcla.
Menor interferencias eléctricas del distribuidor por lo que se mejora la fiabilidad del funcionamiento del motor, las bobinas pueden ser colocadas cerca de las bujías con lo que se reduce la longitud de los cables de alta tensión, incluso se llegan a eliminar estos en algunos casos como ya veremos.
Mayor margen para el control del encendido, por lo que se puede jugar con el avance al encendido con mayor precisión.
A este sistema de encendido se le denomina también de "chispa perdida" debido a que salta la chispa en dos cilindros a la vez, por ejemplo, en un motor de 4 cilindros saltaría la chispa en el cilindro nº 1 y 4 a la vez o nº 2 y 3 a la vez. En un motor de 6 cilindros la chispa saltaría en los cilindros nº 1 y 4, 2 y 5 o 3 y 6. Al producirse la chispa en dos cilindros a la vez, solo una de las chispas será aprovechada para provocar la combustión de la mezcla, y será la que coincide con el cilindro que esta en la carrera de final de "compresión", mientras que la otra chispa no se aprovecha debido a que se produce en el cilindro que se encuentra en la carrera de final de "escape".
A este sistema de encendido se le denomina también de "chispa perdida" debido a que salta la chispa en dos cilindros a la vez, por ejemplo, en un motor de 4 cilindros saltaría la chispa en el cilindro nº 1 y 4 a la vez o nº 2 y 3 a la vez. En un motor de 6 cilindros la chispa saltaría en los cilindros nº 1 y 4, 2 y 5 o 3 y 6. Al producirse la chispa en dos cilindros a la vez, solo una de las chispas será aprovechada para provocar la combustión de la mezcla, y será la que coincide con el cilindro que esta en la carrera de final de "compresión", mientras que la otra chispa no se aprovecha debido a que se produce en el cilindro que se encuentra en la carrera de final de "escape".

Suscribirse a:
Entradas (Atom)